本記事は篠原さんによって書いていただいた製作記です。
篠原翼と申します。
名前の影響なのか、小さい頃から飛行機やロケットが大好きで、大学では航空宇宙工学を専攻しておりました。
大学在学中にモデルロケットという火薬を使ったロケットの競技会で日本チャンピオンになった後、世界大会にも出場したことがあります。
会社員時代は大手自動車メーカーで駆動系部品の設計部隊の取りまとめ業務をしており、その後独立して現在はAVIATOL(アビエートル)という空を舞台にした製品を開発するブランドを運営しております。
主に3D CADの基礎は会社員時代に学ぶことができていました。
ただインターフェース等が異なるので、Fusion 360の基礎はスリプリ様の『Fusion 360 操作ガイド』を使って学びました。
アドバンス編からは自分に必要そうなところだけ読んで、他に足りないところは主にインターネットで検索をかけて勉強しました。
もちろん『Fusion 360 BASE』のページも参考にさせていただいています。
それでもわからないところはメイカーズファクトリーさんに相談しました。
今回は木製のロケット型フロアランプ『The GAZE(ザ・ゲイズ)』を作ろう、というプロジェクトです。
きっかけは自分の部屋に変わった照明がインテリアとして欲しいと思っていたことで、
なんとなく高さは40cmくらいがいいな、と思っていました。
2年前にメイカーズファクトリーさんのレーザーカッター講習会を受講した際に、同じようなスタイルのパーツを組み合わせて作る照明を製作しました。
その時に私もやってみようと思い、今回のプロジェクトが始まりました。
その後、本格的な構想が始まったのはアメリカ旅行へ行く飛行機の中です。
大風の影響で成田空港から飛行機が飛ばず、地上に駐機していた時に大まかなデザインが出来上がりました。
帰ってきてからレーザーカッターが使える場所を探し、さらに様々な機材が使えるというところから、TechShop Tokyoさんにお世話になることにしました。
ロケット型フロアランプ外観の作り方としては、
ロケットの形状の基となる線をIllustratorで描画
↓
原型のロケットを3Dで製作
↓
パーツデータをIllustratorで作成
↓
パーツデータを3Dで作成
↓
3Dで組み合わせをチェック
↓
パーツの切り出し
↓
組み立て
という流れです。
データ作成にはFusion 360の他にAdobe Illustrator CCやAUTODESK® INVENTOR®を使いました。
原型のロケットには綺麗に見えるように黄金比などの秘密が様々なところに隠されており、形には特にこだわりを持っています。
今回は割愛しましたが、途中、製作した原型のロケット周りの空気の流れが気になってしまったので、学生の友人に頼んでANSYS® Fluentで流体解析を行ったりもしています。
その結果は、ロケット本体とサブをつなぐ翼のような部分とそれぞれのつなぎ目のフィレットにリバースエンジニアリングされています。
また外観の木枠の中にプラスチックでできたシェードがあるのですが、当初はありませんでした。
1号機を友人に見せた時に、シェードがあったほうがいいとアドバイスをいただき製作することにしました(ちなみに今回紹介するのは3号機)。
色々考えた結果、CNCで型を作り、その型にプラスチックを熱で柔らかくしたものを真空成形する、という手法をとりました。
CNCと真空成型機もTechShopにある機材を使っています。
実際に出来上がったロケット型フロアランプはウォルナット材の外装で、高さが42cm程度、E17口金対応の電球が使用できる高級感があるランプに仕上がりました。
ロケットの中に電球を入れることができ、電球へのアクセスも簡単に行える構造は初めて見せる人には驚かれます。
(留め具のパーツが外装のデザインの一部でもあり、外装の空間にはまりロックできる)
作品の製作とは直接関係がないのですが、Fusion 360の「図面」機能を使い、Illustratorと組み合わせることで、先の構造の特許出願と外観の意匠権出願の図面を作成でき、昨年末に権利化することもできました。(図面機能で描画できた斜視図)
操作手順を説明します。
◆オリジナルのロケット形状を製作
まずは、元になるロケットの3Dデータを作成します。
①Illustratorでラフな形状を描き、DXFファイルに書き出します。
綺麗な曲線を描く際には、自分はFusion 360でスケッチを描くよりIllustratorのペンツールの方が操作しやすかったため、Illustratorを使用しました。
②挿入コマンドから①のDXFファイルを読み込みます。
③軸を中心に回転させロケットの本体とサブの形状を新規部品で製作します。
④スケッチの翼部分の両端に断面を構築し、それぞれ断面の形状を描きます。
⑤ロフトからそれぞれの断面を選択し、レールを設定してから繋ぎます。
⑥作成したサブと翼のパーツを選択し、円形パターンでその他の2つを作成します。
⑦全てのパーツを結合し、フィレットをかけて完成です。
◆外装パーツの製作
続いて、外装パーツを作ります。
まずは実際に使うウォルナット材をレーザーカッターにかけ、テストカットを行って切り出す時のパラメータ(パワーと速度)を決めました。照明外枠パーツの切り欠き部分の寸法を決めるため、少しずつ切り欠きの大きさを変えたパーツを切り出して組み合わせる予備実験を繰り返し行ないました
予備実験が終わると、3Dモデルのロケットからレーザーカッターで切り出すパーツデータを作成します。
①完成像を想像しながらIllustratorで部品形状を描きます。
②翼の部分にある翼型パーツはFusion 360で製作した3DモデルをAUTODESK INVENTORに読み込み、断面形状を抽出しIllustratorに読み込みます。
Fusion 360では上手く操作ができなかったので、INVENTORを使い断面形状の抽出を行いましたが、Fusion 360でも同じことができるはずです。
③Illustratorで作成したデータをFusion 360に読み込ませ、3Dで組み立ててみて整合が取れているか確認します。
事前に確認することで、材料の無駄を無くすことができます。
④5mmの厚さに挽いたウォルナットの板に防炎耐水などの加工を行い、レーザーカッターにかけて外装パーツを切り出します。
TechShopに置いてあるtrotec社製のSpeedy 300は、加工スピードが早く、正確な動きが特長で使いやすいです。
◆シェード部品の製作~型の作成
続いて、シェード部品を作成します。シェード部品は型を作って作成するため、CNCで削っています。
①外装部品の内側に沿うようなラインをIllustratorで作成したデータから抽出して、Fusion 360で型の3Dデータを作成、つなぎ目が隠れるよう8等分しておきます。
②直方体のデータを作成してシェードパーツのデータを切り取り、ジグのデータを8つ作成します。
③CNC加工機で切削し、型を製作します。作成したジグの3DデータをSRP Playerに読み込ませて、切削条件を決めて切削データを作成する。
TechShopにあるRoland MODELA PROⅡMDX-540はSRP Playerというソフトが付属しており、加工材の3Dデータ(STLデータ)をそのまま読み込ませることで、CAMデータを作成しなくてもCNC加工をすることができます。
④Roland MODELA PROⅡMDX-540にジグの材をセットし、切削データ作成時に決めたエンドミル(刃)をセットして切削を行います。
⑤CNCで加工した型に、空気が通るような小さな穴を電動ドリルで開けておきます。
◆シェード部品の製作~ジグの作成
続いて型をセットするためのジグの2.5D加工データを作成します。
今回、そのままの型を真空成形機にセットすると抜き勾配がないので材と型がくっついて取れなくなるため、型のまわりを囲うようなジグを作ることで解決をすることにしました。
①ジグがセットできるように少し大きめの穴を開けたジグの3DデータをFusion 360で作成します。
②3Dデータを作るために描いたスケッチを書き出します。
③書き出したスケッチをShopbot®(CNCルーター)専用ソフトV Carveに読み込ませ、加工データを作成します。
実際に材を加工しジグを製作します。
①V Carveで作成した加工データをShopbotに読み込ませて加工を行います。
②加工したままだと傾斜の部分が滑らかではないので、ヤスリを使って仕上げます。
◆シェード部品の製作~真空成形機
真空成形機でシェードパーツを作成します。
①ジグに型をセットします。
②型をセットしたジグを真空成形機の中の台に置き、上のバインダーにプラスチック材を挟み固定します。
③ヒーターを固定したプラスチックの上から当て、プラスチック材を所定の時間熱します。
④ブザーが鳴ったらレバーを引いてセットしたジグを持ち上げます。
⑤吸引ボタンを押し、空気を吸ってプラスチック材を型に沿わせます。
⑥必要な部分を切り出してシェードパーツが完成です。
◆組み立て
◆完成!
この作品を製作する上で一番重要なポイントは、完成予想を思い描いた上で、どういう作り方で作るかを事前に考えておくことだったと思います。
今後の展望としては、反響が大きければ、今回紹介したロケット型ランプの量産を考えています。AVIATOLのFacebookページのフォロワーが300人を超えたらクラウドファンディングで資金調達を考えますので、ご興味ある方はFacebookページへのフォローをお願いします。
またAVIATOL・AVIATOL facebookにはロケット型フロアランプの写真が今回紹介した他にも掲載していますので、チェックをしていただけると嬉しいです。
また、ロケット型ランプのミニチュア版を製作キットとして販売できるように開発も進めています。製作や販売、開発にご協力してくれる方も大募集中です!
上の写真がミニチュア版ロケットランプ(高さ約20cm)
著作 篠原
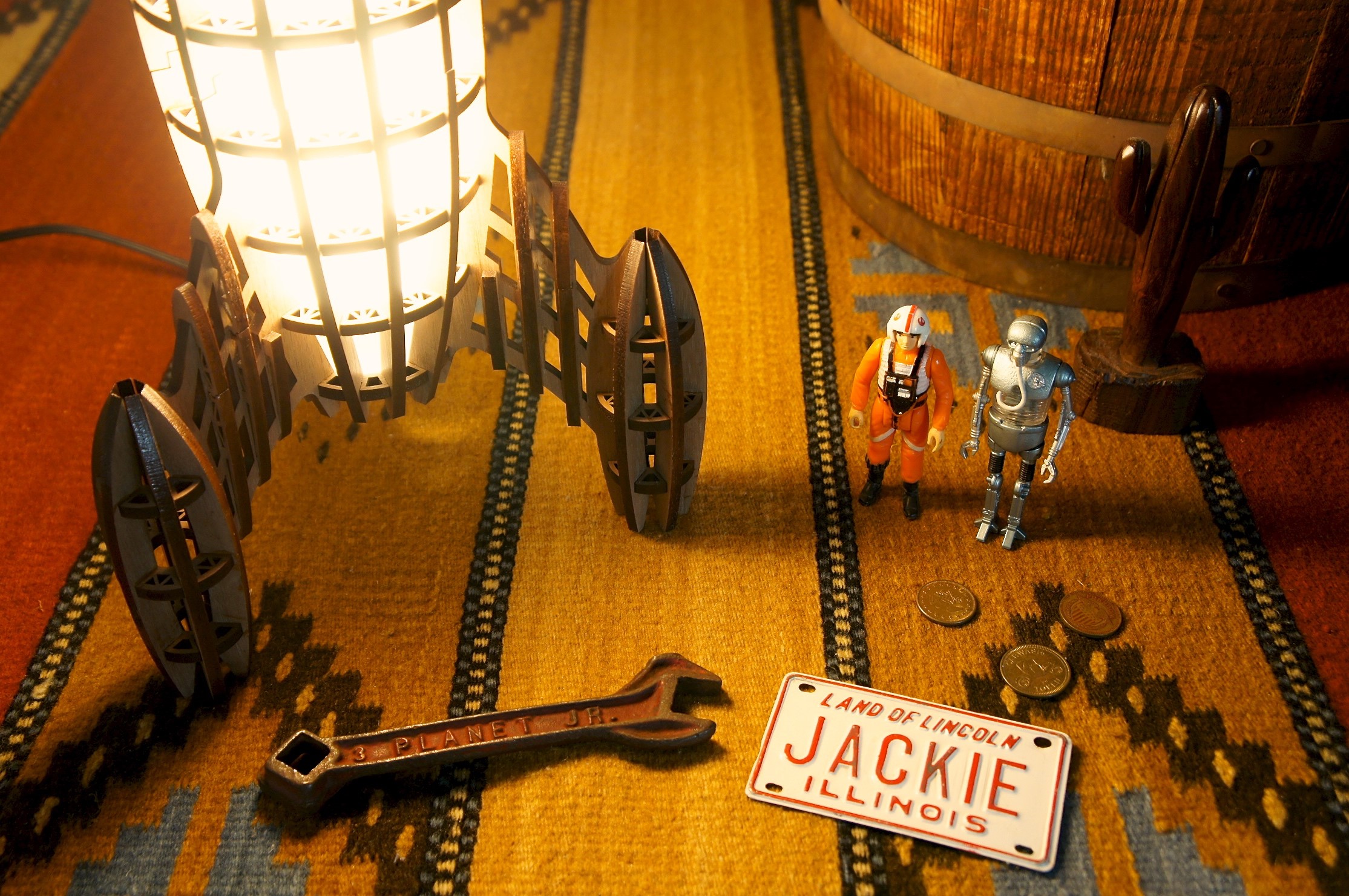